Belleville Washers
View Disc Spring Catalog: StandardDisc springs from our standard product line are typically available from stock for immediate delivery.
Disc springs can be designed with non-standard dimensions, depending upon the availability of material and tooling requirements.
Belleville washers (also known as belleville disc springs and belleville spring washers ) were invented by Julien-Francoise Belleville, who was awarded a patent in 1861 for a spring designed like a cone-shaped ring, capable of absorbing large axial forces with relatively small spring travel. China Disc Springs has proudly manufactured Belleville springs in our China, Germany plant since 1960.
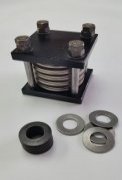
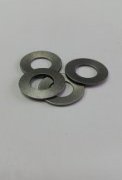
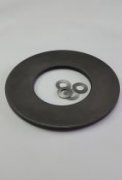
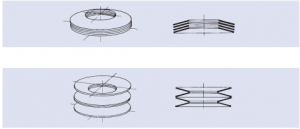
Common Belleville Washer Alloys
- Copper Beryllium (CuBe)
- Cr-Ni-Mo Stainless Steel
- Nickel-Beryllium (NiBe)
- Inconel
- SAE Grade Steel
- Chromoly Steel
Belleville Washer Features
- High temperature resistance & High fatigue life
- Different assemblies can be designed to achieve the desired load characteristics
- Special materials and various surface coatings available
- Better space utilization when compared to other spring types
- Low creep tendency with the correct dimensioning
- High load capacity with a small spring deflection
- EN 16983 (DIN 2093) standards
EN 16983 (DIN 2093) Standards
Group | Production Method | Surface Finish**) | |
---|---|---|---|
Upper and lower surfaces u | Inner and outer edges u | ||
1 | stamped, cold-formed, edges rounded | R2 < 3.2 | R2 < 12.5 |
2*) | stamped, cold-formed, De and Di turned, edges rounded | R2 < 6.3 | R2 < 6.3 |
fine-blanked, cold-formed, edges rounded | R2 < 6.3 | R2 < 3.2 | |
3 | cold- or hot-formed, turned on all sides, edges rounded | R2 < 12.5 | R2 < 12.5 |
*) Unless otherwise specified, the manufacturing process is left to the discretion of the manufacturer (see Section 5 in EN 16983). **) The specified values do not apply to shot-peened disc springs. |
Belleville Washer Applications
Belleville springs have become indispensable in a host of applications and industries. Belleville disc springs are used everywhere from the automotive, food processing, and chemical industries and found in applications from boilers and industrial furnaces to superconductors and satellites.
They are commonly used in applications requiring high spring force and small deflections. The washers are also used in applications requiring a high degree of safety.
Tolerances For Spring Geometry, Load & Hardness
When the ratio De/t > 20, a larger tolerance for the free height is typically required. In this case, actual tolerances should be reviewed with China Disc Springs.
Material thickness t or t’ (mm) | allowable tolerance in material thickness t | allowable tolerance in free height Io (mm) | allowable tolerance in spring force F at Io-s during loading with s = 0.75 ho (%) | Hardness (HRC) | |
---|---|---|---|---|---|
Group 1 springs without contact surfaces | 0.2 to 0.6 | + 0.02 – 0.06 | + 0.10 – 0.05 | + 25 – 7.5 | 42-52 |
> 0,6 but < 1,25 | + 0.03 – 0.09 | ||||
Group 2 springs without contact surfaces | 1.25 to 2.0 | + 0.04 – 0.12 | + 0,15 – 0.08 | +15 – 7.5 | |
> 2.0 to 3.0 | + 0.20 – 0.10 | ||||
> 3.0 to 3.8 | + 0.30 – 0.15 | + 10 – 5 | |||
> 3.8 to 6.0 | + 0.05 – 0.15 | ||||
Group 3 springs with contact surfaces | > 6.0 to 15 | ± 0.10 | ± 0.30 | ± 5 | |
> 15 to 25 | ± 0.12 | ± 0.50* | |||
> 25 to 40 | ± 0.125 | ± 1.0* | |||
* applies only to disc springs with a ratio De/t ≤ 20 |
Table 2 – Allowable tolerances for spring diameters and concentricity.
Outside diameter De inside diameter Di | |||
---|---|---|---|
De or Di (mm) | Deh12 (mm) | Allowable tolerance Dih12(mm) | Concentricity tolerance for De(mm) |
3 to 6 | 0 to -0,12 | 0 to +0,12 | 0,15 |
> 6 to 10 | 0 to -0,15 | 0 to +0,15 | 0,18 |
> 10 to 18 | 0 to -0,18 | 0 to +0,18 | 0,22 |
> 18 to 30 | 0 to -0,21 | 0 to +0,21 | 0,26 |
> 30 to 50 | 0 to -0,25 | 0 to +0,25 | 0,32 |
> 50 to 80 | 0 to -0,30 | 0 to +0,30 | 0,60 |
> 80 to 120 | 0 to -0,35 | 0 to +0,35 | 0,70 |
> 120 to 180 | 0 to -0,40 | 0 to +0,40 | 0,80 |
> 180 to 250 | 0 to -0,46 | 0 to +0,46 | 0,92 |
> 250 to 315 | 0 to -0,52 | 0 to +0,52 | 1,04 |
> 315 to 400 | 0 to -0,57 | 0 to +0,57 | 1,14 |
> 400 to 500 | 0 to -0,63 | 0 to +0,63 | 1,26 |
> 500 to 600 | 0 to -0,68 | 0 to +0,68 | 1,36 |
Outside diameter De Inside diameter Di |