Belleville Disc Spring Combinations – Designing Your Stack
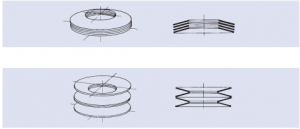
Top: Parallel disc spring stack. Bottom: Series disc spring stack.
Belleville Disc Springs are used as modular components. A group of individual Disc Springs stacked facing the same way is called a parallel spring stack. A group of individual Disc Springs that are stacked facing alternate ways is called a series spring stack. Disc Springs can be combined in many different ways to form stacks in parallel, series, or a combination of both. In a parallel spring stack, the deflection of the stack is equal to that of the individual spring. The load at a given deflection is proportional to the number of individual springs in the stack. In a series spring stack, the deflection of the stack is the sum of the deflections of the individual springs. The load of the stack is equal to the load on the individual spring.
Progressive characteristic load curves can be obtained with the use of parallel stacks having different number of Disc Springs combined to yield compound series stacks (high friction) or series stacks comprised of individual Disc Springs of varying thickness and overall height (low friction). The progression is achieved because the weaker stack – or weaker spring – is cancelled out and thus no longer contributes to the compression of the stack after reaching either the flat position or the deflection limiter.
The following guidelines should be considered in the design of Disc Spring stacks:
- Individual springs stacked in series are used if the deflection of the individual spring is not sufficient.
- Single springs stacked in parallel are used if high loads have to be obtained in a limited mounting space.
- A large spring diameter enables a low overall height to be achieved.
- Normally no more than 4 springs should be stacked in parallel since the discrepancies between the calculated and measured characteristic load curves increase with multiple number of Disc Springs due to friction.
Both series and parallel Disc Spring stacks should be guided. This is done by rods, sleeves, self- centering devices, or by hardened wire segments. Internal and external guides should be polished over their entire length, and hardened to at least 55 HRC. In the case of purely static or rarely alternating loads, an un-hardened guide element can be used. In Belleville Disc Spring stacks, the load can be applied via either the inner or the outer diameter. If the load is applied via the inner diameter, the contact pressures will be higher.
The internal and external guides require some clearance between the spring stack and the guide element. This allows adequate room for the displacement of the lubricant while ensuring proper guidance.